汽车储能BMS模块——NTC温度采集
2025.07.08
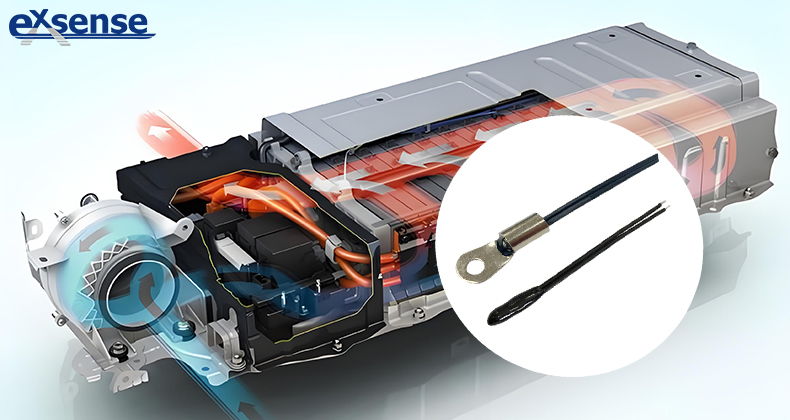
作为新能源汽车动力系统的核心技术之一,BMS(电池管理系统)构成了保障电池系统稳定运行、延长电池使用寿命及守护车辆安全的技术基石。而NTC温度传感器作为BMS系统中不可缺少的感知元件,承担着电池温度监测、热管理补偿及故障预警诊断等核心功能。凭借其高可靠温感及反馈能力,NTC温度传感器为电池温控系统构建了可靠的安全防线,有效提升电池运行的稳定性与耐久性,成为推动电动汽车技术迭代与产业化发展的重要技术支撑。
一、BMS工作原理
储能电池管理系统(BMS)的工作原理其核心在于对电池组数据的全方位监控、处理与控制,旨在确保电池性能的最优化与安全无忧。首先,BMS借助高精度NTC温度传感器,实时捕捉电池单体在电压、电流及温度等多个维度的关键数据。在数据采集之后,BMS运用复杂的算法对数据进行深入剖析。
二、NTC温度传感器原理解析
NTC 温度传感器本质上是一种热敏电阻型温度探头,基于负温度系数效应,其电阻值会随温度升高呈指数级下降。这类传感器通常由两种或三种金属氧化物,混合在类流体粘土介质中,经高温烧结工艺,在窑炉内形成致密陶瓷体结构。
在实际应用中,利用NTC热敏电阻在恒定功率下,电阻值与温度的相关换算规则,通过精确测量电阻值变化,即可反推对应温度,从而实现温度的精准检测与闭环控制。该特性使其成为温度监测与控制系统中的核心元件。
三、AFE 芯片——温度采集
AFE(Analog Front End,模拟前端电路),构成连接模拟温度传感器与数字信号处理系统的桥梁,是BMS(电池管理系统)实现电芯安全监测的关键元件。AFE 芯片集成多路采样通道,可同步采集电芯电压、温度等关键参数,其内部架构主要由均衡开关、通信模块、采集模块构成。其中,采集模块包含模拟开关(MUX)、模数转换器(ADC)、参考源(REFERENCE),其功能架构如图详细解析:
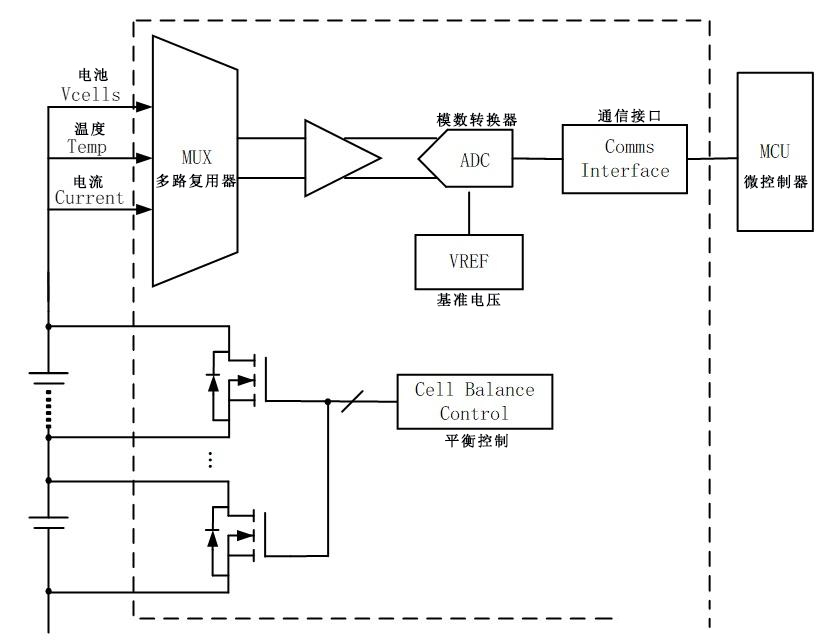
在数据采集过程中,模拟信号经模拟开关(MUX)选择性采样后,由模数转换器(ADC)转换为数字信号,最终通过 API/IIC/UART 等多个通信接口传输至主控制器(MCU) 。MCU根据这些数据信号,实时计算荷电状态(SOC)、健康状态(SOH)等核心参数。此外,AFE 还具备电池工况动态监测能力,通过实时调节电池参数,保障电池始终处于最优工作区间,有效延缓电池老化,确保电动汽车稳定运行。具体功能细分如下:
▉电压检测通道:直接获取电池组中单体电芯电压数据,并同步承担电芯均衡任务,确保各电芯电压一致性。
▉NTC温度传感器接口:NTC热敏电阻作为锂离子电池热管理核心器件,可精准捕捉充放电过程中的温度变化。传感器部署于电池组温度敏感区域,将温度信号转化为电压信号后传输至 AFE。
▉GPIO连接器:提供外部功能扩展接口,支持冷却系统、接触器控制、加热装置等设备的接入,可通过固件升级灵活拓展功能。
▉ISO-SPI 通道:构建传感器电路与控制电路间的高速隔离通信链路,确保数据传输的可靠性与安全性。
▉AFE电源模块:为AFE芯片提供稳定工作电压,通常直接从电池组取电,保障供电可靠性。
四、BMS用NTC温度传感器的选型与布置要点
在NTC温度传感器的选型过程中,需综合考量温度测量范围、精度等级、响应特性等核心参数,确保其性能适配BMS系统的高标准需求。例如,高温场景下需选择耐温范围覆盖电池组极端工况(如快充/高温环境)的传感器;高精度需求场景则需优先考虑误差范围更小的产品;而对于动态温度变化频繁的电池模组,响应时间更短的传感器能有效提升温度监测的时效性。
除选型外,传感器的布置位置同样至关重要。需结合电池组拓扑结构、热管理策略及散热特性进行精细化布局——既要避免因靠近散热通道(如风扇、冷却板边缘)导致温度测量值偏低,也要防止因埋入电池内部过深而影响信号传输效率。通过科学规划,确保NTC温度传感器能够精准捕捉电池本体及各区域(如电芯间隙、母线连接点)的实时温度状态,为BMS的热管理决策提供可靠数据支撑。
总结:综上,新能源汽车的BMS系统与NTC温度传感器构成电池管理的核心感知与控制单元。二者通过协同运作实现电池状态的全天候监测、动态评估与精准调控,为电池安全运行筑牢防线(如过温预警、热失控预防),有效延长电池使用寿命。